Modern machines and processes designed by machine builders and system integrators that integrate hydraulics are increasingly using high levels of electrohydraulic control. These electrohydraulic control systems are often required to synchronise multiple hydraulic rams, reconfiguring them at the touch of a button to handle different tasks or form part of a closed loop system, controlling force and displacement. As a result, hydraulic ram manufacturers and refurbishers are increasingly being asked to include position transducers with the hydraulic rams to facilitate electrohydraulic control for industrial applications.
One of the fundamental challenges of electrohydraulic control is accurately knowing the position of rams. This is typically achieved with a linear position transducer (or sensor) that can be either mounted internally or externally to the cylinder depending on the requirements of the application. The transducer comprises two main parts: the transducer rod with separate magnet attached to the cylinder head, and the transducer head which houses all of the electronics required to interpret the movement and turn it into a usable output.
Fitting the transducer internally is the favoured mounting method where space is limited and a transducer that is specifically designed to be mounted inside a cylinder (such as the MTS Temposonics R Series) is required. A hole is drilled down the centre of the piston rod to accommodate the sensor rod and the piston head is machined to accommodate the ring magnet along with the cylinder end cap which is machined to accommodate the transducer head. As the piston head moves along the stroke of the piston bore, so does the magnet which in turn causes the output of the sensor to vary with length.
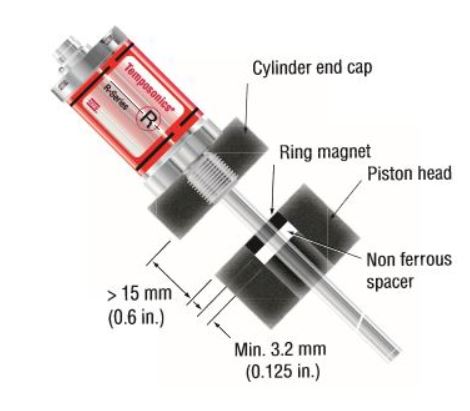
Alternatively, mounting the transducer alongside the cylinder eliminates the time, effort and expense of machining, but exposes the transducer to the environment. A protective enclosure can be used to shield the transducer from certain hostile conditions, but many applications generally benefit from integrating the transducer into the relatively safe confines of the cylinder.
The increasing demand for measuring ram position with a transducer to facilitate electrohydraulic control has required leading hydraulics and engineering services companies to quickly understand how position transducers can be integrated into their products and services.
One such company is AM Hydraulics and Engineering Services in Birmingham. Founded in 1978, AM Hydraulics specialises in hydraulic ram refurbishment with a capacities of up to 20 tons and they are increasingly being asked to provide in-cylinder position measurement to facilitate electrohydraulic control . Satty Cooner, Manager at AM Hydraulics explained how they recently called on Emolice during a critical cylinder refurbishment, “we were looking to partner with a position specialist that could advise us not only on the most suitable technology and product to measure ram position, but who also had significant in house mechanical design expertise to work with us on the transducer integration and testing.
Emily Quinn, Marketing Manager at Emolice added: “ We are the UK distributor and technical partner for MTS Temposonics who manufacture a wide range of in-cylinder transducers that are perfect for both manufacturers and for retro fitment. Our in house application engineers were able to advise on the most suitable in cylinder transducer from MTS Temposonics’ extensive product range and through our in house mechanical engineers we were also advise on the best way to modify the cylinder to accommodate the sensor.”
By combining their hydraulics expertise with that of position specialists Emolice, AM Hydraulics are finding additional opportunity with new customers that require electrohydraulic control.
To find out more about the MTS range of sensors visit: https://emolice.com/mts-temposonics/